The frequency of inspection and maintenance for excavator track rollers can vary depending on several factors, including the operating conditions, the intensity of use, and the manufacturer’s recommendations. However, as a general guideline, it is recommended to inspect and maintain excavator track rollers on a regular basis, which can be determined by the number of operating hours or the duration of usage.
Here are some general recommendations:
Regular Visual Inspections: Conduct visual inspections of the track rollers at the end of each workday or shift. Look for signs of wear, damage, misalignment, or loose components. Pay attention to any unusual noises or vibrations during operation, as these can also indicate potential issues with the track rollers.
Lubrication: Follow the manufacturer’s guidelines for lubrication intervals and procedures. Proper lubrication helps minimize friction, reduce wear, and extend the lifespan of the track rollers. Ensure that the lubricant used is compatible with the excavator’s specifications.
Cleaning: Keep the track rollers clean by removing dirt, debris, and mud regularly. Accumulated debris can accelerate wear and affect the performance of the track rollers. Use appropriate cleaning methods, such as using compressed air, water, or brushes, while taking care to prevent the entry of water or contaminants into sealed areas.
Periodic Maintenance: Perform more comprehensive maintenance tasks at recommended intervals, which can vary depending on the manufacturer’s guidelines or specific excavator model. This may involve disassembling and inspecting the track rollers, replacing worn components, and ensuring proper alignment.
Track Adjustment: As part of regular maintenance, adjust the track tension as needed. Improper track tension can cause excessive wear on the track rollers and other undercarriage components. Follow the manufacturer’s recommendations for proper track tensioning.
Component Replacement: Replace track rollers or worn components when they no longer meet the manufacturer’s tolerances or exhibit significant signs of wear, damage, or deterioration. Prompt replacement helps maintain the stability, traction, and overall performance of the excavator.
It’s important to note that these recommendations are general guidelines, and specific maintenance intervals and procedures can vary. Always refer to the manufacturer’s guidelines and consult the excavator’s service manual for accurate and detailed maintenance instructions specific to your excavator model. Additionally, factors such as extreme operating conditions or heavy usage may require more frequent inspections and maintenance.
What are the main components of an excavator track roller?
The main components of an excavator track roller typically include:
Roller Body: The roller body is the main structure of the track roller. It is usually a cylindrical or drum-shaped component that supports the weight of the excavator and the tension of the track chain. The roller body is designed to rotate smoothly on a shaft or bushing.
Shaft or Axle: The shaft or axle is a central component that runs through the roller body and provides a rotating axis. It is typically made of high-strength steel and is responsible for transmitting the load and torque from the track chain to the roller body.
Bearings: Bearings are used to support the shaft or axle within the roller body and facilitate its smooth rotation. These bearings can be ball bearings, needle bearings, or bushings, depending on the design and manufacturer’s specifications.
Seals: Seals are used to prevent the entry of contaminants, such as dirt, water, and debris, into the roller body and bearings. They help maintain the lubrication and protect the internal components from premature wear and damage.
Lubrication Fittings: Lubrication fittings, also known as grease fittings or zerk fittings, are commonly found on excavator track rollers. carrier roller excavator manufacturer These fittings allow for the injection of grease or lubricant into the roller body to reduce friction and wear between the components.
Retaining Rings: Retaining rings or circlips are used to secure the bearings on the shaft or axle. They prevent the bearings from moving axially and ensure proper alignment and functioning of the roller assembly.
Mounting Hardware: Mounting hardware, such as bolts, nuts, and washers, is used to attach the track roller to the undercarriage frame or other components of the excavator. These components ensure secure and stable attachment of the track roller.
Wear Pads or Flanges: Some track rollers may have wear pads or flanges attached to the roller body. These pads or flanges help guide and support the track chain, reducing lateral movement and wear.
These are the main components of an excavator track roller, and their specific design and configuration may vary depending on the excavator model and manufacturer. Regular inspection, lubrication, and maintenance of these components are essential to ensure optimal performance, longevity, and reliability of the excavator’s undercarriage system.
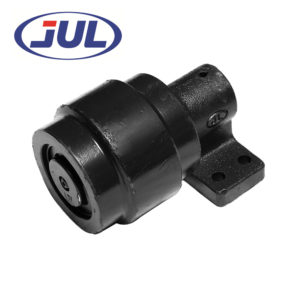